Sometimes even the smartest powder specialists at Harro Höfliger are tearing their hair out. For example, when due to particle shape or size, stability or density, the material to be filled simply cannot be dosed into the designated capsule or cavity of the blister strip.
For Dr. Karlheinz Seyfang, Principal Consultant at Harro Höfliger, these stubborn powders are precisely what makes his work so exciting, and ducking the issue is not an option: “Changing formulations post approval is not possible,” he explains. “We must work with them the way they are – the same applies to the target containers. This is why the product determines the process. Ultimately, we find a solution for everything.”
Tricky powders
These are some of the most stubborn materials:
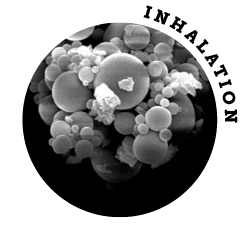
Hollow microspheres have an extremely low density (< 0.03 g/ml). For comparison: The density of sugar is 20 times higher. Despite their spherical shape, the particles only have a moderate flow rate and are sensitive to high relative humidity.
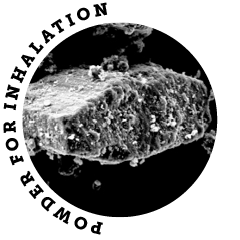
Such formulations consist of active substances in the form of small “crumbs” which are attached to carrier crystals of lactose monohydrate. In a powder inhaler, the active ingredient particles must detach from the carrier. Unfortunately, this can already happen during the dosing process which bears the risk of de-mixing.
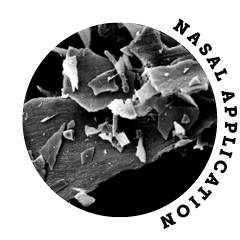
Lyophilized formulations clump together when relative humidity is too high. In addition, the flow properties of the powder are negatively affected by the unfavorable particle shape: The flakes can mechanically interlock.
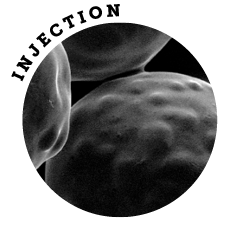
Polymer beads with an embedded active ingredient must not be damaged, as that would change the release rate. This formulation is injected, so filling must be aseptic. Due to the high material value of the product, it has to be possible to completely empty the machine’s dosing system.

Silver oxide for coating wound dressings is an accumulation of extremely fine particles. The interparticle adhesion forces cause the material to flow poorly, as it tends to clump together and stick to machine parts during processing.
The appropriate dosing system
The search for solutions starts with the right dosing system. In most cases, specialty machines by Harro Höfliger are equipped with volumetric dosing systems. Dr. Seyfang: “We often work with very small dosing quantities which have to be filled into small target containers – some with a filling level of 100 %. This is a real challenge when it comes to powders with particle sizes smaller than 10 µm.”
With these tiny particles, the interparticle adhesion forces are predominant. The material flows very poorly, clumps, and adheres to the surfaces of the machines that come into contact with the product.
In order to find out how powders behave during processing, their properties are determined in the Harro Höfliger laboratory where, among other things, their impact on the flow behavior is examined. This is then put to the test on table-top versions of common filling systems.
“Once a suitable system has been found, we scale up to a production machine.“Dr. Karlheinz Seyfang, Principal Consultant at Harro Höfliger
Here, we can already see on a small scale what can later lead to problems on a large scale. If powders flow poorly, the dosing chamber will not be filled properly. Vibrating devices, ultrasound or picking up the powder with suction under negative pressure can help. Dr. Seyfang: “Our table-top dosing systems already meet many requirements, and once a suitable system is found, we scale-up to a production machine.”
Suitable framework conditions
Knowing the powder properties is not just important for exact dosing. Powders and processes also have to harmonize so that later they run smoothly on the machine. More than 90 percent of the projects that Harro Höfliger is involved in, relate to medicines and medical products. Their stability must be guaranteed over the entire storage and administration period.
This can only be ensured if the manufacturing conditions are right. For example, the share of biopharmaceuticals containing proteins and peptides as active ingredients is increasing. They are often used as lyophilizates or spray-dried powders which can only be processed in an environment with low relative humidity in order to prevent clumping.
If the relative humidity is too low, static charges may occur: The dosing processes are then difficult to control since the powder particles repel each other or stick to the dosing system. Dr. Seyfang: “This is just one of many balancing acts that we have to master. When dealing with difficult substances, we sometimes have to develop new, individual solutions. We are a specialty machine manufacturer for that very reason – to meet those extraordinary challenges.”
Download this article as PDF file
Photo: Janine Kyofsky