It has become one of the largest health issues in the world: According to a WHO report, about half of all patients with chronic diseases do not take their medication as prescribed. This lack of therapeutic adherence or “compliance” not only negatively affects patients. It is estimated that in the US alone the subsequent cost amounts to at least 100 billion dollars a year – a heavy burden on the healthcare system.
Tiny rods with great potential
Subcutaneous implants promise to potentially improve this situation. These are active substance-containing rods of polymer compounds that are placed under the patient’s skin with a device. Depending on the field of application, they release their active ingredient evenly over a period of up to several months. This can replace the daily intake of tablets or recurrent injections. Moreover, in many cases the implants are biodegradable, i. e. they dissolve completely in the body. The range of applications is broad: Currently, the rods are already used in oncology, in the treatment of opiate dependence, or as contraceptives.
Everything from a single source
As with all implants, it is imperative that the rods containing the active ingredient are sterile in order to avoid risks for patients. Cooperating with specialized technology partners enables Harro Höfliger to offer customers a comprehensive solution and supply implants, device components and machines for aseptic assembly from a single source.
The company provides support from the initial product idea. “We consider all components and make sure that aseptic processing is feasible. For conducting sterilization tests we can establish contacts with specialized partner companies,” says Ulrich Stahl, Director New Technologies at Harro Höfliger.
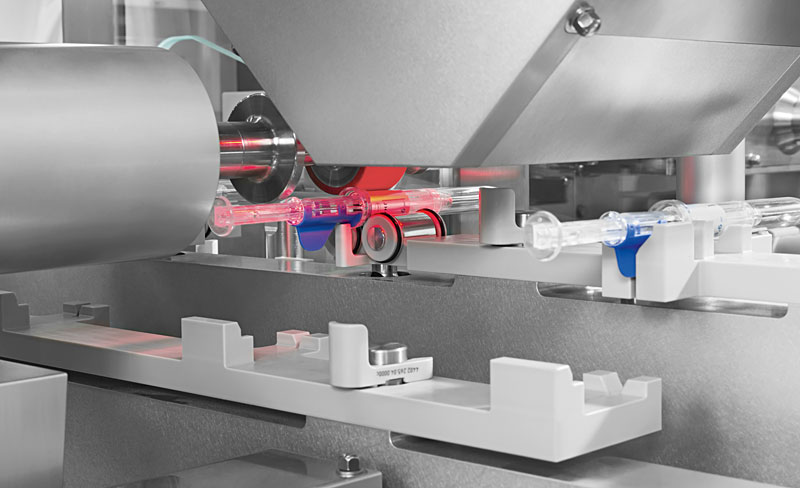
Precise positioning of a laser-printed label on the device.
If interested, customers can also receive support in the development of trays for feeding the individual parts during assembly: “For past projects, our specialists have provided specific advice on the design and functionality of the thermoformed workpiece carriers. Aseptic procedures have very particular requirements. And when it comes to successful process development, customers can always count on the support of our Engineering & Innovation Service Team,” explains Stahl.
Even while the device is assembled and fitted with the implant, various measures ensure that a sterile environment is maintained. For example, optimized motion sequences of the gripper systems minimize the dispersion of airborne particles. In addition, laminar air flow systems with sterile filters are used. Last but not least, “mock-ups” – true-to-scale wooden models of the entire machine – offer additional safety and reliability since they can be used to simulate and optimize all insertion processes and manual operation procedures on the machine prior to design approval.
“An administration form with a future”
One of Harro Höfliger’s technology partners covering the production of sterile implants is Thermo Fisher Scientific. Marc Hofrichter reports on the product’s potential and the manufacturing challenges.
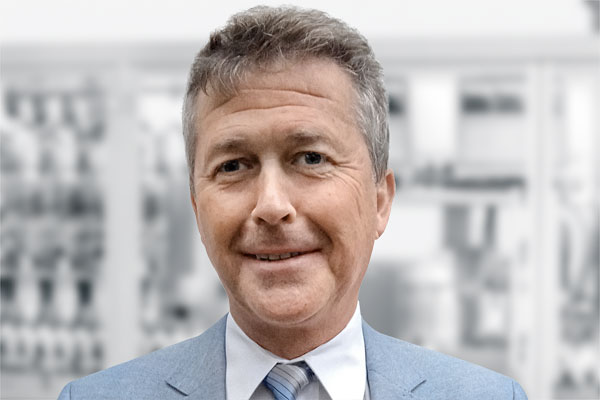
Marc Hofrichter, Project Manager Customized Projects, Thermo Fisher Scientific
Mr. Hofrichter, in which areas are subcutaneous implants used?
The fields of application are almost unlimited: Whether in ophthalmology, the treatment of schizophrenia and cancer, contraception or the delivery of opiates, hormones and antibiotics – subcutaneous implants are used in all these areas. Meanwhile, even in veterinary medicine there is a strong interest in this administration form.
Are there any special challenges during production?
Not only is it important to process these highly potent and sensitive materials safely and carefully, but also to ensure high-precision length and diameter tolerances as well as excellent surface quality. Another major challenge is to guarantee the precise distribution of active ingredients with the tightest tolerance limits in a fully automated manufacturing process – which includes measuring, trimming and sorting. With the Thermo ScientificTM Pharma mini Implant Line, we are well equipped to meet these challenges.
How do you see the future of the market?
In recent years we have noticed an increasing interest in implants as drug depots and in our implant line. Therefore, I am convinced that this is an administration form with a promising future.
About Thermo Fisher Scientific
Thermo Fisher Scientific is one of the world’s leading partners in serving science, with revenues of more than 20 billion dollars and about 70,000 employees. It is their mission to enable their customers to make the world healthier, cleaner and safer. Through their premier brands Thermo Scientific, Applied Biosystems, Invitrogen, Fisher Scientific and Unity Lab Services, the company offers an unmatched combination of innovative technologies and comprehensive services.
Download this article as PDF file
Illustration: Thomas Heller, Photo: Helmar Lünig