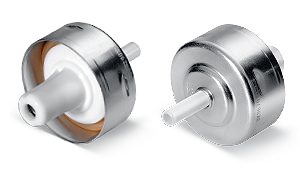
Each dosing valve must be precisely matched to the requirements of the individual customer and their pharmaceutical formulation.
The Metered Dose Inhaler (MDI) is a prime example of a device that looks simple to the final patient, but this is part of its elegance. The valve itself contains seven parts, including two soft seals and a spring. However, also unknown to the end user, is the technology and customisation that goes into each format to suit individual customers and pharmaceutical formulation’s requirements. It has been so successful that, worldwide, almost one billion cans are used every year. Sadly, global rates of respiratory disease seem to be on the rise so there will, if anything, be even more asthma inhalers in future.
State of the art camera inspection strategy
Originally the valves were made manually on scatter boards by manual shaking. Later automatic assembly equipment was introduced and now Bespak by Recipharm have taken the next step with Harro Höfliger with a machine at a higher speed range, higher cleaning standards.
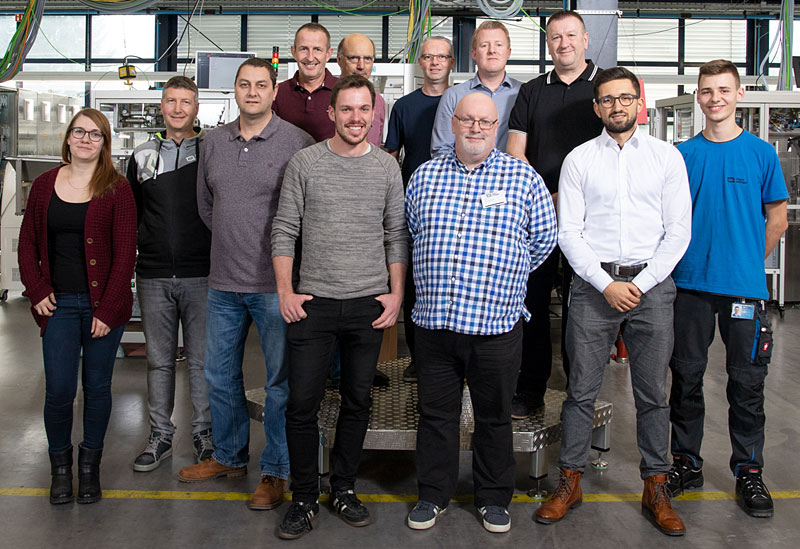
In November 2019 the teams of Bespak by Recipharm and Harro Höfliger met personally in Allmersbach im Tal.
Additionally, Harro Höfliger developed and installed a state of the art camera inspection strategy that is much more sophisticated than that previously in use. Finally, the machine has to cope with all the different formats that different drug formulations are likely to require. At the end of last year, the machine went into operation in King’s Lynn – and is helping to ensure that patients all over the world can breathe freely.
About Bespak by Recipharm
Bespak by Recipharm delivers market leading design, development and manufacture of drug delivery devices to the global pharmaceutical market. This includes inhaler, nasal technologies and auto-injectors as well as development and manufacturing services.
Download this article as PDF file
Photo: Helmar Lünig