Medicines containing highly potent substances must be safe, and not just for patients. Already during the production of such medicines, for example for use in cancer therapies, machine operators must be protected as best as possible from any contact with the product. This aspect is of particular importance to the pharmaceutical and chemical company Merck.
Jeffrey Campbell, Director of Engineering MRL, Pharmaceutical Sciences at Merck New Jersey reports about the beginning of the cooperation with Harro Höfliger: “In our search for a capsule filling machine with the highest operator protection, the Modu‑C Containment caught our attention.” It was specifically developed for the testing of new active ingredients as well as the production of small batches with toxic and highly potent substances.
”In our search for a capsule filling machine with the highest operator protection, the Modu‑C Containment caught our attention.“Jeffrey Campbell, Director of Engineering MRL, Pharmaceutical Sciences at Merck New Jersey
“Initial dosing tests in Harro Höfliger’s cleanrooms showed that the machine is ideally suited for our product,” reports Jeffrey Campbell. “Immediately afterwards, we made a reference visit to a Swiss company who already works with a similar system from Harro Höfliger. We had the opportunity to study handling, cleaning, and interfaces in operation directly on site and to talk to the operators. After that, it was clear that this was the right concept for us too.”
One machine – two new developments
The basic machine design was now found – but Merck had two special requirements: First, a guarantee that no powder dust would remain on any capsule after leaving the machine. Second, Merck wanted to enable their machine operators to clean the machine without the need for a reliance on personnel protective equipment.
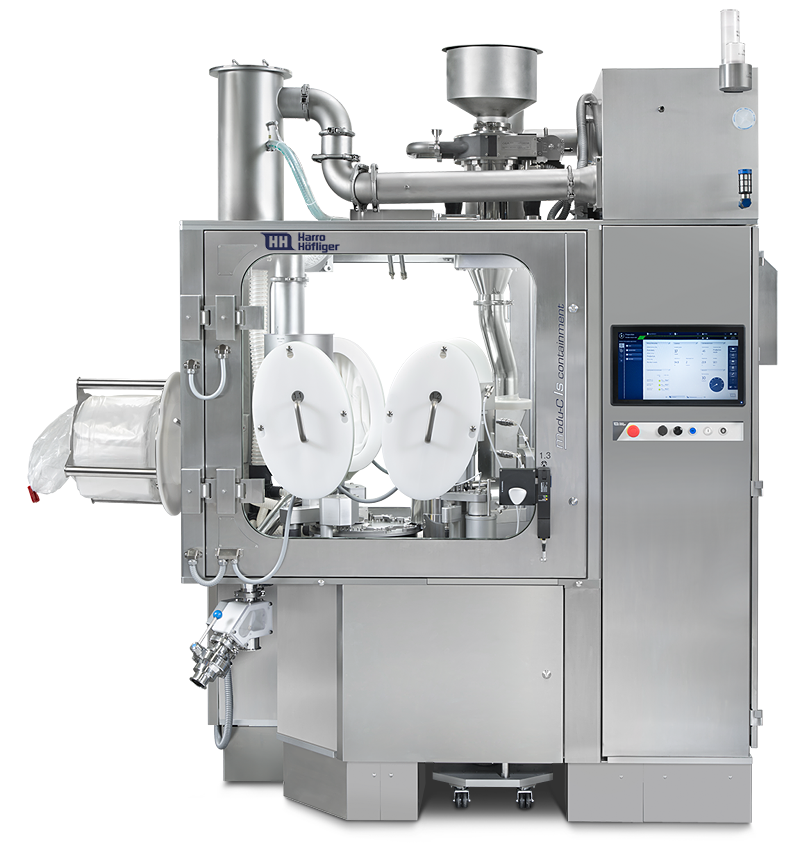
For Merck, Harro Höfliger equips the Modu‑C LS Containment capsule filling machine with two special functions for cleaning and capsule dedusting.
In order to remove powder dust from the capsule shell, many companies rely on an external capsule deduster. “However, the important thing for us was to save space in the cleanroom. Harro Höfliger therefore developed a deduster that is directly integrated into the machine,” says Jeffrey Campbell.
In this deduster station, each filled capsule passes several ring brushes, which remove even the smallest amounts of powder mechanically. Philipp Hoffmann, Mechanical Design Engineer at Harro Höfliger: “After development of the station was completed, we first tested it with very sticky whole egg powder. This showed that our in-house development can keep up with external dedusters.”
”After development of the station was completed, we first tested it with whole egg powder. This showed that our in-house development can keep up with external dedusters.“Philipp Hoffmann, Mechanical Design Engineer at Harro Höfliger
With the newly developed fogging station, the experts fulfilled the request for cleaning without the need for a reliance on personnel protective equipment. Philipp Hoffmann explains what makes this station special: “With fogging, operators do not initially have to open the machine door. Instead, they wet the production area via glove ports with purified water, using a manual hand spray gun. Alternatively, the spray mist can also be generated automatically by nozzles inside the machine. Product dust is bound in the process. The containment can then be opened for the actual cleaning, without blowing up dust.”
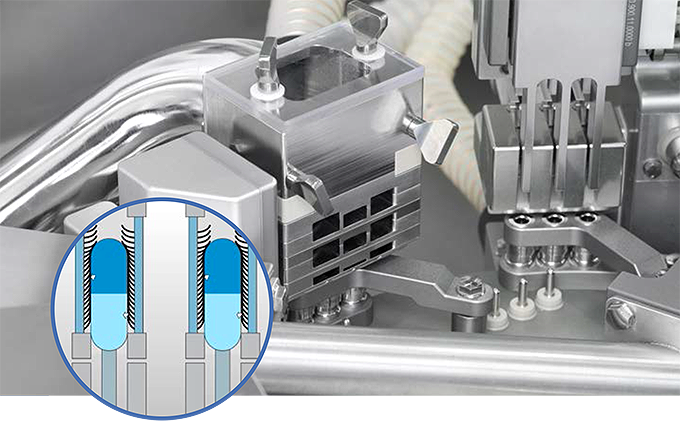
Deduster stationThe dedusting process takes place inside the Modu‑C machine. In the deduster station, each filled capsule passes several ring brushes which remove even the smallest amounts of powder mechanically.
Factory Acceptance Test from a distance
When the machine, which was designed according to the UL safety standards applicable in the US, was ready for shipment, an acceptance test of a special kind was scheduled. Jeffrey Campbell: “Due to the COVID-19 travel restrictions, there was no way we could be present at the Factory Acceptance Test. Harro Höfliger therefore positioned two cameras on site: One provided the overall view of the machine, the other the view into the interior. Via livestream, we were able to attend the test comfortably from New Jersey – and convince ourselves across the Atlantic of the impeccable operation of our new system.”
About Merck
Merck, a leading science and technology company, operates in the fields of healthcare, life science and performance materials.
Around 58,000 employees work to make a positive difference to millions of people‘s lives every day by creating more joyful and sustainable ways to live: From developing precise genome-editing technologies to discovering unique ways to treat diseases, all the way to providing applications for smart devices – Merck is everywhere. In 2020, Merck generated a turnover of 17.5 billion euros in 66 countries.
Download this article as PDF file
Photos: Helmar Lünig, Merck, Janine Kyofsky