Quietly buzzing servo-controlled shuttles speed around a central oval on guide rails – the so-called tracks. They accelerate, decelerate, group and arrange themselves with the components or products they have picked up before reaching the downstream processing station. At the end of this fascinating choreography there is a perfectly assembled auto-injector which allows patients to administer their drugs with a precise dose.
With its new intelligent transportation system, the tried-and-tested MOT assembly platform offers significantly more flexibility in production. Individually controllable shuttles based on linear drives move individual parts and the end product quickly and flexibly from one station to the next. Magnetic force keeps the highly dynamic transport vehicles securely on track. The system software always ensures sufficient safety clearance between the shuttles and prevents them from colliding. Special track switches enable agile splitting and merging of product streams. This flexibility also gave the new Harro Höfliger assembly platform its name: MOT Flex.
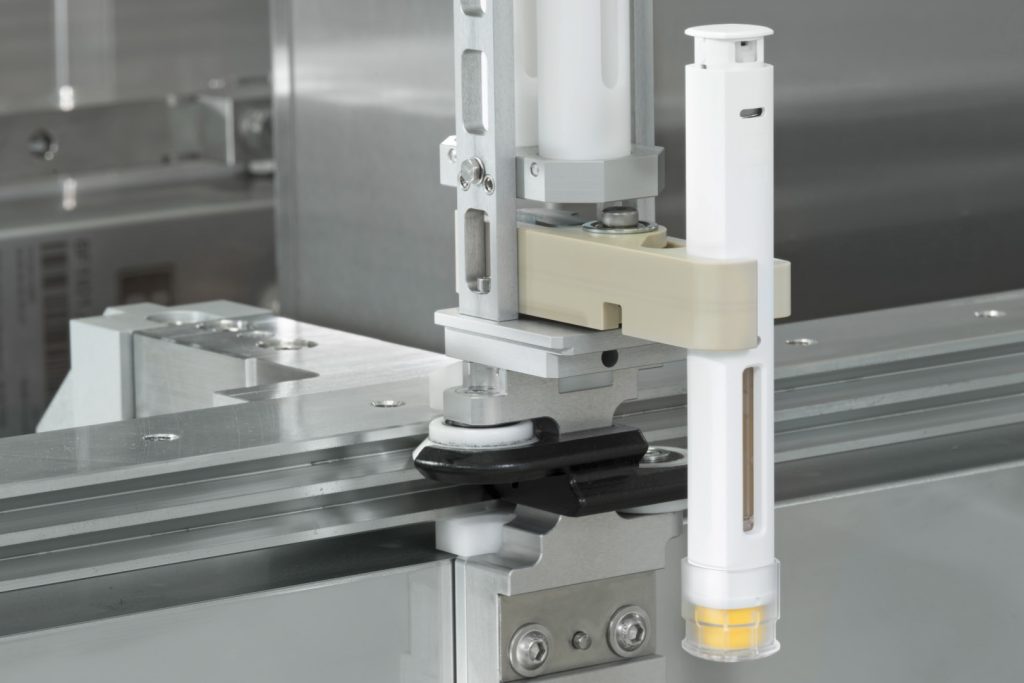
Magnetic force holds the individual shuttles on the guide rails.
“The drive system offers us a multitude of new options and has what it takes to fundamentally change the design and operation of production lines,” says Rainer Wolbers, Operations Director Assembly Technologies. “The MOT Flex is characterized by a small footprint and an economical workflow. The infeed and outfeed of products can also be reconceptualized, because it is possible to connect trayloaders and palletizers directly to the intelligent transportation system without pucks.”
varying speed
Format changeovers can be carried out much more easily and quickly than with conventional chain drives. This allows for assembly of diverse medical and pharmaceutical devices, such as pen injectors, auto-injectors, inhalers and many more, on one line. “Depending on requirements, parallel processing stations, buffer zones and much more can be realized for our customers,” Rainer Wolbers explains. “The capability of varying speed and acceleration between processing stations allows the shuttles to be distributed to multiple stations in time-critical processes. The effort required for less demanding tasks like presence monitoring, however, can be kept to a minimum.”
“The transportation system sets completely new standards in terms of flexibility.“Rainer Wolbers,
Operations Director Assembly Technologies at Harro Höfliger
The new MOT Flex with the innovative shuttle system was first used in a line for the final assembly of auto-injectors. The core task in this project was to insert the drug-prefilled syringes into the syringe housing with high precision and to press them in reliably according to the manufacturer’s instructions. Printing the auto-injector with laser technology was also part of the process. Special attention was paid to efficient handling and gentle, smooth transport of the syringe without any glass-to-glass contact.
On this line, two robotic arms accurately grip the pre-assembled syringe units from the tray, which is fed via Harro Höfliger’s TS Pallet Euro palletizer, and places them in the shuttles. These speed along with their transported load to the first processing station. Here the syringe unit is separated again and the drive unit for triggering the injection is removed in order to insert the prefilled syringe. Then the device is reassembled in the steps to follow. After the subsequent quality control, the nimble transport vehicles deliver the fully assembled auto-injectors back to the robot station: The gripper arms carefully pick up the end products and load them in the finished trays, which are automatically placed on pallets.
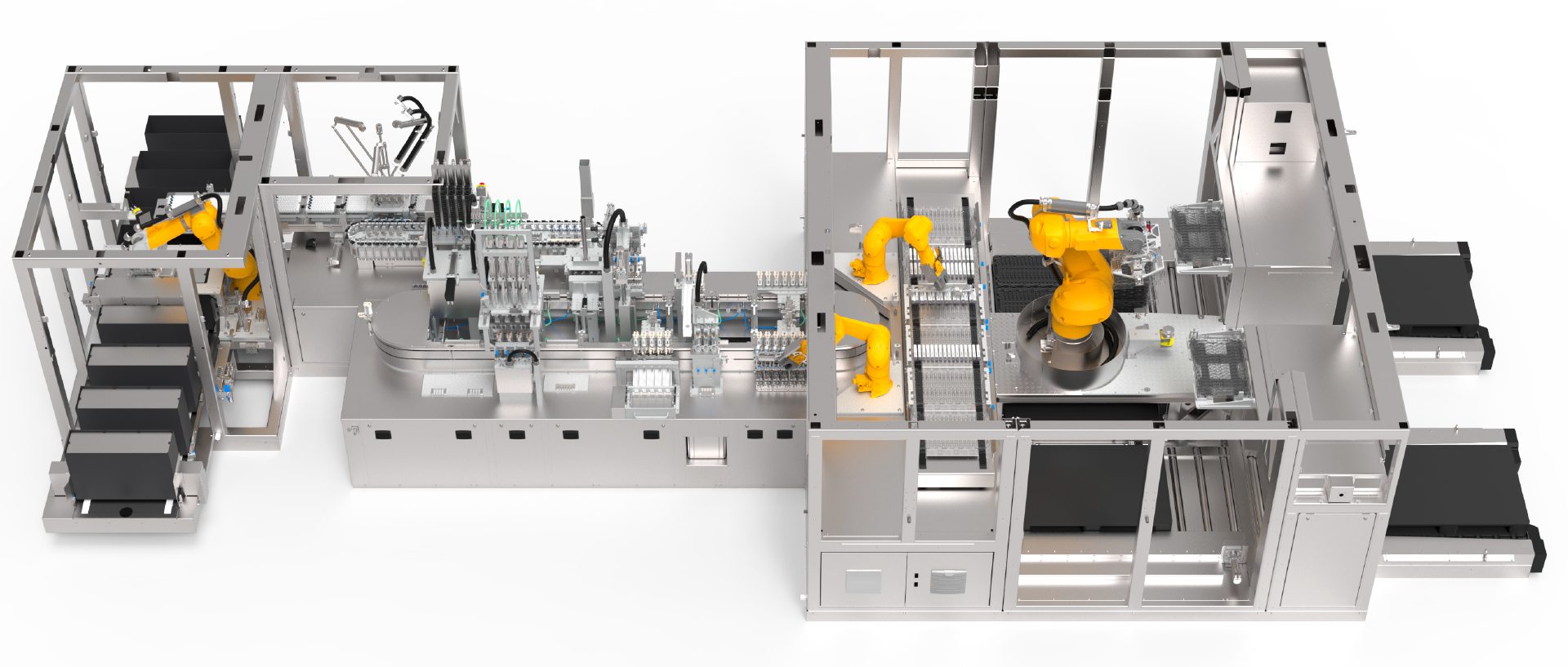
The new drive technology enables a very compact design. Trayloaders and palletizers can be linked directly without pucks.
Multiple options
The shuttles have already started the next round and are whizzing around the oval with a new load. “The transportation system sets completely new standards in terms of flexibility,” says Rainer Wolbers. “This makes it easier than ever to assemble completely different products on one line.”
Download this article as PDF file
Photos: Helmar Lünig