Herr Jung, was hat es mit dem Umbauprojekt auf sich?
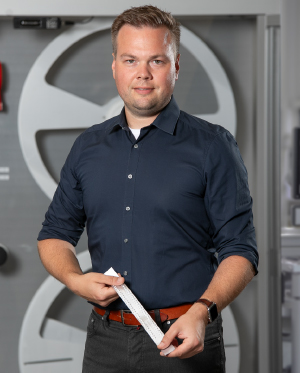
Benjamin Jung, Account Manager Customer Service bei Harro Höfliger, begleitete die Modernisierung der MSP.
Nachhaltigkeit und ein verantwortungsvoller Umgang mit Ressourcen werden immer wichtiger. Dazu gehört es auch, Maschinen möglichst lange zu nutzen – und trotzdem zukunftsfähig zu bleiben. Als Customer Service liefern wir verschiedenste kundenspezifische Lösungen, um den Lebenszyklus von Anlagen zu verlängern oder sie auf neue Anforderungen anzupassen. Modernisierungen und Upgrades jeglicher Art, von Retrofits bis zu kompletten Maschinenumbauten, gehören selbstverständlich dazu. Der Umbau der MSP – einer Maschine zur Befüllung von Blistern mit Inhalationspulver – bei der AEROPHARM GmbH war das bislang größte Projekt dieser Art, das wir im Customer Service realisiert haben.
Was war konkret gefordert?
Die MSP mit Walzen-Dosiersystem hatte jahrelang zuverlässig ihren Dienst getan und Blisterstreifen für einen Trockenpulver-Inhalator mit wirkstoffhaltigem Pulver befüllt. Aufgrund eines Produktwechsels hatte unser Kunde die Anlage vor Längerem außer Betrieb genommen. Ich betreue dieses Pharmaunternehmen seit rund 15 Jahren in unterschiedlichen Positionen bei Harro Höfliger. Bei einer Tasse Kaffee kamen Pierre Solcher, Head Service & Qualification, sowie Dr. Sebastian Moritz, PD Group Head, und ich darauf zu sprechen, ob es möglich sei, mit einem neuen Füllsystem und der Nachrüstung von Optionen der Anlage neues Leben einzuhauchen. Es war möglich, wie sich zeigte!
Wie sind Sie vorgegangen?
Meine Kollegen und ich haben uns die Anforderungen genau angeschaut. Die Anlage besteht aus drei Modulen: Formen, Befüllen/Siegeln, Schneiden. Mit der Umrüstung von drei Walzenfüllern auf ein neues Dosiersystem galt es, ein Modul komplett zu ersetzen und Anpassungen bei den anderen Stationen vorzunehmen. Auch sollte auf Wunsch des Kunden Platz für ein optional nachzurüstendes X-Ray-System zur Füllkontrolle innerhalb des Containments geschaffen werden – dies bedeutete eine Verlängerung der Anlage um 1,5 Meter. Zur Dosierung hatten wir ein anderes unserer am Markt etablierten Füllprinzipien im Blick, welches in der Lage ist, die speziellen Anforderungen der AEROPHARM GmbH zu erfüllen. Um zu ermitteln, ob dies die optimale Dosierlösung für das Produkt darstellte und welche Formatteile nötig waren, gingen wir im Prinzip vor wie bei einer neuen Maschine und ließen unsere Pharma Services Pulveranalysen und Abfüllversuche mit aktivem Material im Reinraum machen.
Wo fand der Umbau statt?
Ein Logistikunternehmen brachte die Anlage zurück nach Allmersbach in das Werk, in dem sie einst aufgebaut worden war. Das Projektmanagement lag beim Customer Service und wir bewerkstelligten Konstruktion, Montage, Elektromontage, Steuerungstechnik und Technische Dokumentation mit eigenen Ressourcen. Trotzdem arbeiteten wir natürlich Hand in Hand mit den verschiedenen Fachabteilungen im Haus, beispielsweise was Validierung, Containment oder Kamerakontrolle angeht. Nach Inbetriebnahme und FAT in unserem Produktionswerk wurde auch der SAT beim Kunden, mit dem wir ausgezeichnet zusammenarbeiteten, erfolgreich abgeschlossen.
„Schon während der ersten Projektphase war klar, dass wir einen kompetenten Partner benötigen, der uns hilft, die komplexen Projektanforderungen umzusetzen. Wir wendeten uns daher an Harro Höfliger – uns verbindet eine langjährige Geschäftsbeziehung. Es dauerte nicht lange und die Idee der Ertüchtigung einer Bestandsmaschine war geboren, wohlwissend, dass dies keine einfache Aufgabe und mit einem gewissen Aufwand verbunden war. Zusammenfassend kann man sagen: Es war die richtige Entscheidung.“Pierre Solcher,
Head Service & Qualification,
AEROPHARM GmbH
Gab es neben den neuen Stationen weitere Änderungen?
Die MSP wurde in diesem Zuge auf eine weiterentwickelte Steuerungstechnologie umgestellt – von PacDrive M auf PacDrive 3 – und beim Bediensystem von HMI 1.0 auf 2.0 aufgerüstet. Das gibt unserem Kunden die Sicherheit, seine Anlage aus heutiger Sicht viele Jahre, ohne eine mögliche Problematik mit abgekündigten Komponenten, nutzen zu können – ein Thema, das uns im Customer Service besonders am Herzen liegt.
Welche Vorteile über die Ersatzteil-Sicherheit hinaus bietet ein Umbau?
Ein Umbau oder ein Retrofit, bei dem eine Maschine bezüglich aktueller Anforderungen verbessert beziehungsweise neu konfiguriert wird, bedeutet eine nachhaltige, zukunftsfähige Alternative zu einer Neuanschaffung und häufig niedrigere Investitionskosten. Bis auf die beschriebenen, komplexen Maßnahmen bei der MSP konnte der Großteil der Anlage unberührt bleiben. Die verlängerte Nutzungsdauer einer Maschine schont nicht nur Ressourcen, sondern reduziert für den Auftraggeber meist auch den Aufwand für die Umschulung des Bedienpersonals, da die vertraute Grundfunktionalität erhalten bleibt. Einer Anlage quasi ein zweites Leben zu schenken, begeistert mich wie auch unsere Expertinnen und Experten vom Customer Service jedes Mal aufs Neue.
„Nicht nur im Hinblick auf den sparsamen Umgang mit Ressourcen, welcher auch für uns eine enorm wichtige Rolle einnimmt, hat uns das Gesamtkonzept überzeugt. Wir wurden durch Harro Höfliger in allen Projektphasen kompetent unterstützt und es wurde stets lösungsorientiert gearbeitet. Wir schauen positiv in die Zukunft und sind für kommende Herausforderungen bestens gerüstet.“
Dr. Sebastian Moritz,
PD Group Head, Pharmaceutical Development,
AEROPHARM GmbH
Diesen Artikel als PDF-Datei herunterladen
Fotos: AEROPHARM GmbH, Helmar Lünig