Oral (ODF) and buccal films (MBF) can be effective aids in the fight against severe pain. Once placed on or under the tongue, the thin ODF strips dissolve quickly and the active ingredient is released. MBF adhere to the oral mucosa and release the active ingredient. First, a polymer matrix containing active ingredients is produced in a special coating process. The PMK production and packaging machines then convert the polymer matrix into strips and package the films into individual pouches. Camera systems carefully monitor every step.

Oral and buccal films are effective aides against pain.
During web conversion, the films are cut length- and crosswise. Typical ODFs are rectangular between two and ten square centimeters in size. MBFs usually have rounded corners for better comfort inside the mouth. A flexo printer, for example, then imprints the active ingredient content and the product name. This is where the first of three image processing modules is used. It checks whether the imprint is correct and easy to read for the patient.
“The challenge is that 1,050 parts per minute pass through the machine at maximum speed. That means almost 18 parts per second,” says Hartwig Sauer, Department Leader Vision Systems at Harro Höfliger. “During this short period of time, we have to take a picture of each product, evaluate it and send the result to the machine control system.” If the camera detects a faulty imprint, the products are marked virtually and ejected at the end of the machine.
“More than half of our machines require camera controls.“Hartwig Sauer, Department Leader Vision Systems at Harro Höfliger
Not a millimeter too small
For the flawless products, the next step is to pack them in 50 x 50 millimeter pouches, primarily made of child-resistant packaging material. To this end, the films are transferred to the lower packaging material web. A camera checks whether the product has the correct geometry – i.e. the exact length, width and contour – and is positioned in the center. If the product were positioned in the sealing area, the pouch would not seal and close properly. In addition, the films are checked for possible contamination by particles, product or packaging material residues.
Prior to sealing, the packaging material web is also printed with a batch number, expiration date and a 2D data matrix code. A third camera station checks for correct printing. “Since these films are often used in pain therapy, it is especially important that all information is accurate and legible. No mistakes can be made here,” explains Sauer.
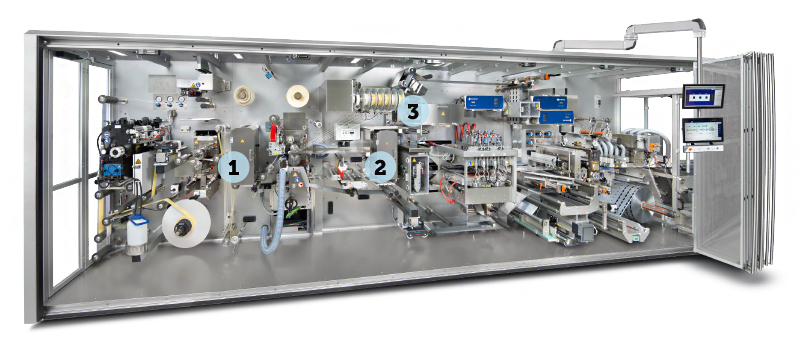
Camera stations monitor every step of the model PMK production and packaging machines:
1 Checking the imprint of active ingredient content and product name
2 Checking the position before packaging into four-side sealed pouches
3 Checking the imprint of the upper packaging material web
Researching the future
Accuracy and process monitoring are also important for other forms of packaging. “More than 50 percent of our machines require camera controls,” says Sauer. “We used to work with external companies, but then our customers always had two different contacts.”
This is now in the past. For the last six years, Harro Höfliger has had its own image processing department. In the camera laboratory, 17 application engineers examine which camera light color and wavelength can be used to best map specific features for subsequent examination of the required test criteria with complex image processing software. They are also conducting research into future technologies such as thermal imaging and deep learning. “In the future this will enable our machines to detect errors better and faster to further improve exact production of medication.”
Download this article as PDF file
Photos: Helmar Lünig, Janine Kyofsky, shutterstock.com/Lyudmyla Ishchenko