Angelo Alletto is a production engineer at Roche Diagnostics in Mannheim and his mission is clear: “His” line number 13 must be running in order to reach the required production output at the end of each week. In other words: 85 cycles per minute, 16 hours a day and ideally without interruptions. “The machine should only stop when we have planned it, not because something has broken,” says Alletto.
With the introduction of a Preventive Maintenance Plan this year, Roche and Harro Höfliger have set out on a shared path to achieve precisely this goal. Roche‘s Elecsys®-Technology has been on the market for about 20 years. Laboratories all over the world use it in many areas of immunology. The successful diagnostic product consists of up to three components in separate plastic bottles, which Roche combines, labels and packages in different ways with Line 13. It is also constantly controlled by numerous cameras, sensors and checkweighers to make sure that only perfectly produced and therefore 100% safe products leave the plant.
“The many combinations and carton formats, as well as various packaging inserts with their tolerances, make the packaging process prone to errors,” says Alletto and adds: “Together with Harro Höfliger‘s Customer Service we have been able to optimize many factors in recent years and in doing so have continuously increased our output.”
14 machines work closely together
Line 13 consists of various machine types and includes trayloaders, an assembly unit, several labelers, carton erectors and a toploader cartoning machine. In addition, the line has numerous feeding and control systems – a complex array of 14 machines that work together in closely timed intervals. Maintaining the entire system in such a way that technical malfunctions can be avoided is what the Preventive Maintenance Plan shall make possible in the future.
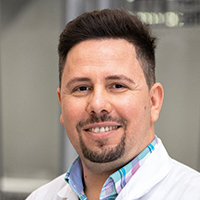
Together with Harro Höfliger, Angelo Alletto, production engineer at Roche, makes sure that “his” Line 13 is running.
“We will no longer use our budget for unscheduled repairs between maintenance intervals, but for preventive and carefully prepared maintenance activities. This enables us to achieve a more stable production process that gives us the time and flexibility to identify and implement further optimization needs,” explains the production engineer.
But there is another reason for planning maintenance more precisely, Alletto knows: “Inspection authorities such as the FDA or even the TÜV (German Technical Inspection Authority) nowadays demand documentation that is more precise and goes far beyond the time of the actual approval. Ticking off maintenance checklists is no longer sufficient.” Thanks to the maintenance plan and the associated documentation, from now on Roche will be able to provide transparent evidence as to which checks and maintenance activities were carried out and when they took place.
Maintenance needs preparation
In order to implement the Preventive Maintenance Plan, some initial preparation is required. In addition to the experience from previous maintenance work and daily operation, an evaluation of the machine serves as a basis. “To this end, all machine components are analyzed by our technical experts and rated with regards to expected wear and tear, the probability of failure and the resulting effects,” explains Sven Fischer, Service Manager at Harro Höfliger. Fischer has been responsible for Roche for many years and has played a key role in advancing the Preventive Maintenance Plan project.

Line 13 consists of a complex construction of different machine types, feeding and control systems.
“We maintain an open and honest communication with our customers. Roche‘s systems receive our utmost attention. As a result, we were able to develop individual solutions together with Roche which made it possible to continually increase production efficiency. We consider the Preventive Maintenance Plan a large sign of confidence and the result of our excellent teamwork,” says Sven Fischer. A cooperation that will become even stronger. “Preventive maintenance is an ongoing process,” explains Angelo Alletto. “Maintenance plans are living documents that we will continually refine and adapt. Together with Harro Höfliger, we are getting better and better and can continue to increase our production.”
About Roche Diagnostics
Roche Diagnostics GmbH is located in Mannheim and is a subsidiary of the Swiss company F. Hoffmann-La Roche AG which is headquartered in Basel. With about 8,300 employees, Roche in Mannheim develops products for people with diabetes or cardiovascular diseases. In addition, the company produces life-prolonging drugs against cancer and important products for in-vitro diagnostics, which are delivered from Mannheim to destinations all over the world.
Download this article as PDF file
Photos: Roche Diagnostics