Mit leisem Sirren sausen servogesteuerte Shuttles auf Führungsschienen – den Tracks – um ein zentrales Oval. Sie beschleunigen, verzögern, gruppieren sich und ordnen sich mit den Komponenten oder Produkten, die sie aufgenommen haben, vor der nächsten Bearbeitungsstation ein. Am Ende der faszinierenden Choreografie steht ein perfekt montierter Autoinjektor, mit dem sich Patientinnen und Patienten ihre Medikamente dosiergenau verabreichen können.
Mit einem neuen intelligenten Transportsystem bietet die bewährte Montageplattform MOT bedeutend mehr Freiheitsgrade in der Produktion. Individuell ansteuerbare Shuttles auf Basis von Linearantrieben bewegen Einzelteile und das Endprodukt schnell und flexibel von einer Station zur nächsten. Magnetkraft hält die hochdynamischen Transportvehikel sicher am Track. Die Systemsoftware sorgt immer für genügend Sicherheitsabstand zwischen den Shuttles und verhindert, dass sie kollidieren. Spezielle Weichen ermöglichen die agile Aufteilung und Zusammenführung von Produktströmen. Diese Flexibilität hat der neuen Montageplattform von Harro Höfliger auch den Namen gegeben: MOT Flex.
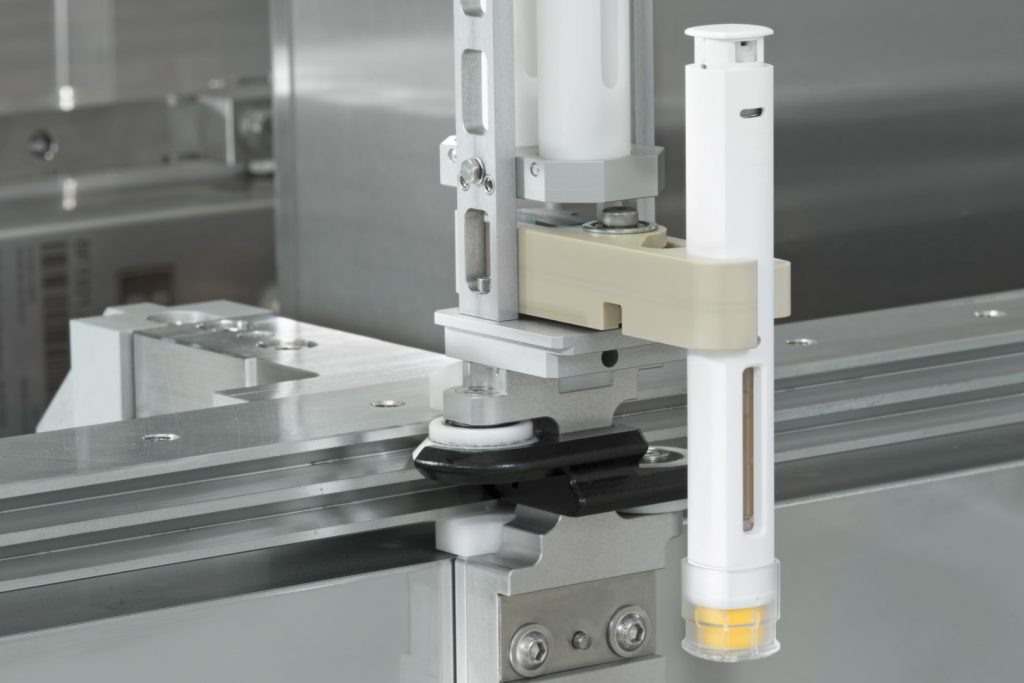
Magnetkraft hält die einzelnen Shuttles an den Führungsschienen.
„Dieses Antriebssystem bietet uns viele neue Möglichkeiten und hat das Zeug, Design und Betrieb von Produktionslinien grundlegend zu verändern“, sagt Rainer Wolbers, Operations Director Assembly Technologies. „Die MOT Flex ist sehr kompakt, macht den Workflow ökonomischer und auch die Zu- und Abführungen von Produkten können neu gedacht werden. Trayloader und Palettierer sind direkt und ohne Pucks mit dem intelligenten Transportsystem kombinierbar.“
Geschwindigkeit variieren
Formatwechsel lassen sich sehr viel einfacher und schneller durchführen als beim konventionellen Kettenantrieb. Auf einer Anlage können unterschiedliche medizinische und pharmazeutische Devices, beispielsweise Pen-Injektoren, Autoinjektoren und Inhalatoren, montiert werden. „Je nach Anforderung sind parallele Bearbeitungsstationen, Pufferzonen und vieles mehr für unsere Kunden realisierbar“, erklärt Rainer Wolbers. „Durch die Möglichkeit, Geschwindigkeiten und Beschleunigungen zwischen den Bearbeitungsstationen zu variieren, lassen sich die Shuttles bei zeitkritischen Prozessen auf mehrere Stationen verteilen. Der Aufwand für weniger anspruchsvolle Aufgaben, etwa für Anwesenheitskontrollen, kann dagegen auf ein Minimum reduziert werden.“
„Wir fahren mit dieser neuen Technologie nicht nur im wörtlichen Sinne mehrgleisig.“Rainer Wolbers,
Operations Director Assembly Technologies bei Harro Höfliger
Ihre Feuertaufe hat die MOT Flex mit dem innovativen Shuttlesystem in einer Pilotanlage für die Endmontage von Autoinjektoren bestanden. Hier war die Kernaufgabe, die mit einem Medikament vorbefüllten Spritzen hochpräzise in das Spritzengehäuse einzusetzen und gemäß den Herstellervorgaben sicher zu verpressen. Auch das Bedrucken des Autoinjektors mit Lasertechnik zählte zu den Prozessen. Besonderes Augenmerk galt dem effizienten Handling und behutsamen Transport der Spritze – es durfte zu keinem Glas-Glas-Kontakt kommen.
Zwei Roboterarme greifen in dieser Anlage zielsicher die vormontierten Spritzengehäuse aus dem Tray, der über Harro Höfligers Europalettierer TS Pallet zugeführt wird, und setzen sie in die Shuttles ein. Diese sausen mit ihrem Transportgut zur ersten Bearbeitungsstation. Dort wird das Spritzengehäuse wieder getrennt und die Antriebseinheit für das Auslösen des Devices entnommen, damit in Folgeschritten die vorbefüllte Spritze eingesetzt und wieder alles zusammengefügt werden kann. Nach der anschließenden Qualitätskontrolle liefern die flinken Transportvehikel die fertig montierten Autoinjektoren zurück zur Roboterstation. Sorgsam nehmen die Greifarme die Endprodukte auf und legen sie in die Fertig-Trays, die automatisch auf Paletten gesetzt werden.

Die neue Antriebstechnik ermöglicht eine sehr kompakte Bauweise. Trayloader und Palettierer sind ohne Pucks mit dem Transportsystem kombinierbar.
Mehrgleisig fahren
Die Shuttles sind in der Zwischenzeit schon in die nächste Runde gestartet und flitzen mit neuer Fracht um das Oval. „Wir fahren mit dieser neuen Technologie nicht nur im wörtlichen Sinne mehrgleisig“, sagt Rainer Wolbers lachend. „Das Transportsystem setzt ganz neue Maßstäbe in Sachen Flexibilität. Es ist damit so einfach wie nie, ganz unterschiedliche Produkte auf einer Anlage zu montieren.“
Diesen Artikel als PDF-Datei herunterladen
Fotos: Helmar Lünig